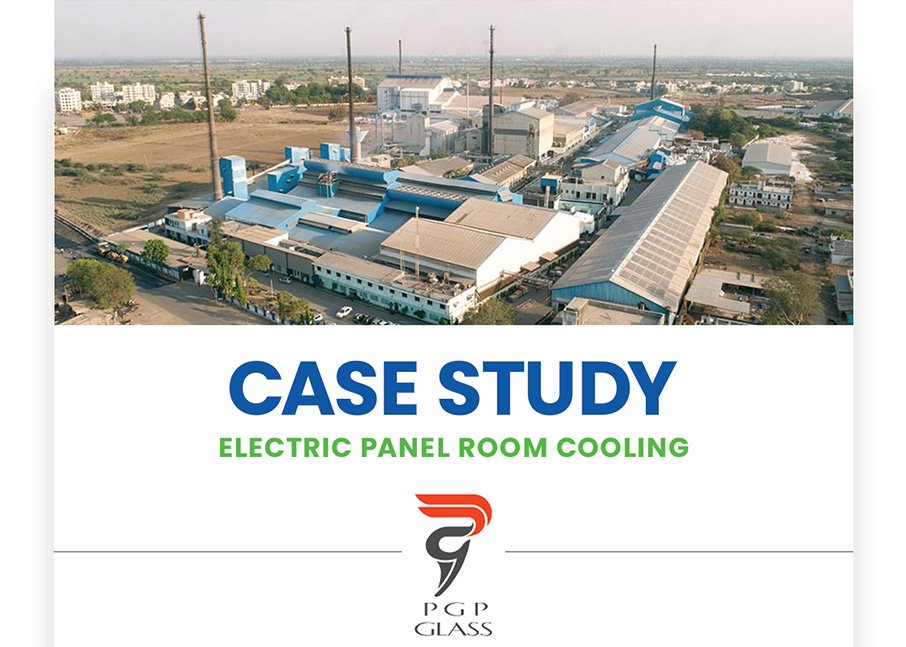
PGP Glass, a global leader in glass bottle manufacturing, operates a large-scale facility in Vadodara, India.
ELECTRIC PANEL ROOM COOLING
PROJECT HIGHLIGHTS
Electricity Cost Savings Per Year
₹4,00,000
Reduced Carbon Footprint
Payback Period
Less than 3 Years
OVERVIEW
One of the critical areas of this facility is the Central Control Room, which houses the electrical panel controlling various operations. With a highly connected load, the room generates significant heat, and maintaining an optimal temperature for the equipment’s smooth functioning was a major challenge. The conventional cooling system installed consumed a considerable amount of energy while struggling to maintain the required temperature and relative humidity (RH)
CHALLENGE
The Central Control Room at the PGP Glass facility is crucial for the plant’s operations, as it controls the entire electrical system. The room, covering 1300 square feet, faced the following challenges:
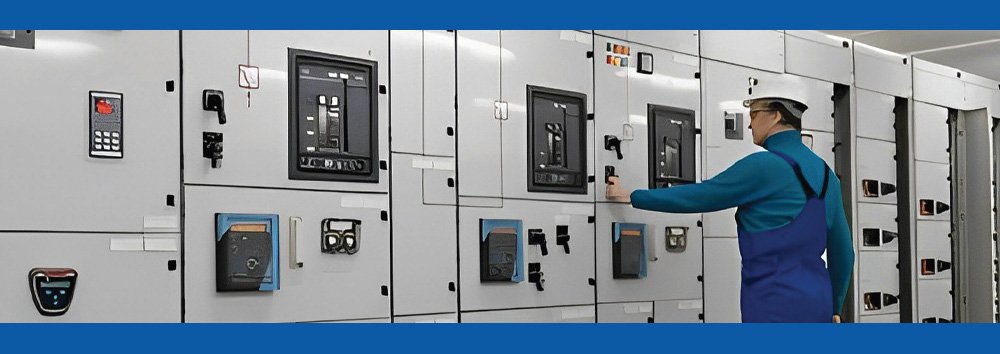
High Heat Load
With an electrical load of 800 KW, the room generated a considerable amount of heat, making it difficult to maintain the desired temperature and relative humidity levels.
Temperature Requirement
The room’s temperature needed to be maintained at 25±3 °C to ensure the optimal functioning of the electrical equipment, with relative humidity below 60%.
Energy Consumption
The existing 34 TR AHU (Ai Handling Unit) system consumed a significant amount of energy, leading to high operational costs. There was an urgent need to reduce energy consumption while maintaining
SOLUTION
Evapoler introduced an Innovative Hybrid Air Conditioning System that effectively addressed PGP Glass’s cooling challenges while reducing energy consumption.
The hybrid system combined traditional cooling technology with evaporative cooling, delivering efficient cooling with reduced power usage.
Key features of the system include:
Total Capacity Installed
15 TR
(Reduced from the previous 34 TR)
Airflow Supplied
15000 CFM
(Cubic Feet per Minute)
was calculated to match the high heat load of the control room.
Hybrid Technology
The system used a combination of evaporative cooling and traditional air conditioning, leveraging the advantages of both systems to deliver energy-efficient cooling.
Evapoler’s hybrid system was designed to cool the air effectively and regulate humidity while using less energy compared to conventional systems.
RESULTS
The implementation of the Hybrid Air Conditioning System in PGP Glass’s Central Control Room delivered outstanding results:
Energy Savings
While the initial calculations estimated a 28% energy saving, actual measurements at the site revealed an even higher savings of 38%.
Temperature Control
The system successfully maintained the desired room temperature, measured at 26 00, ensuring the optimal functioning of the electrical equipment.
Cost Efficiency
The reduction in energy consumption translated into significant cost savings, cutting energy expenses by 35%.
CONCLUSION
The success of this project highlights the potential for hybrid cooling technologies to deliver efficient, sustainable, and cost-effective solutions for industrial facilities with high cooling demands.
PGP Glass’s experience serves as a model for other companies in energy-intensive industries looking to optimize their cooling systems and reduce their environmental footprint.
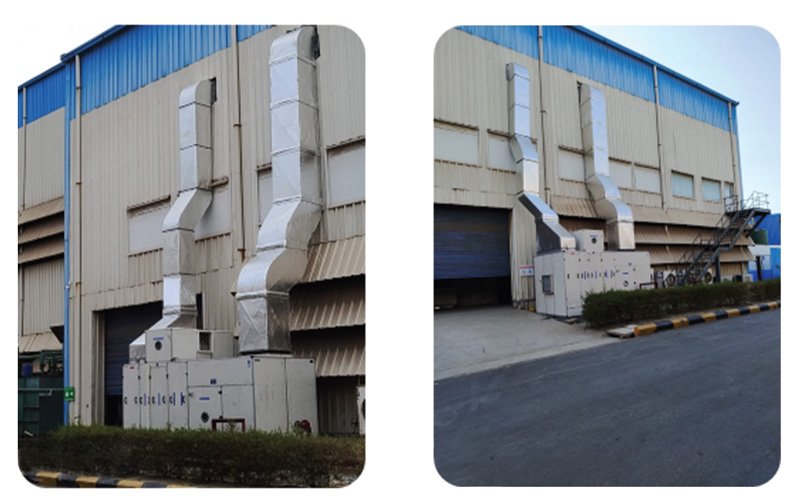