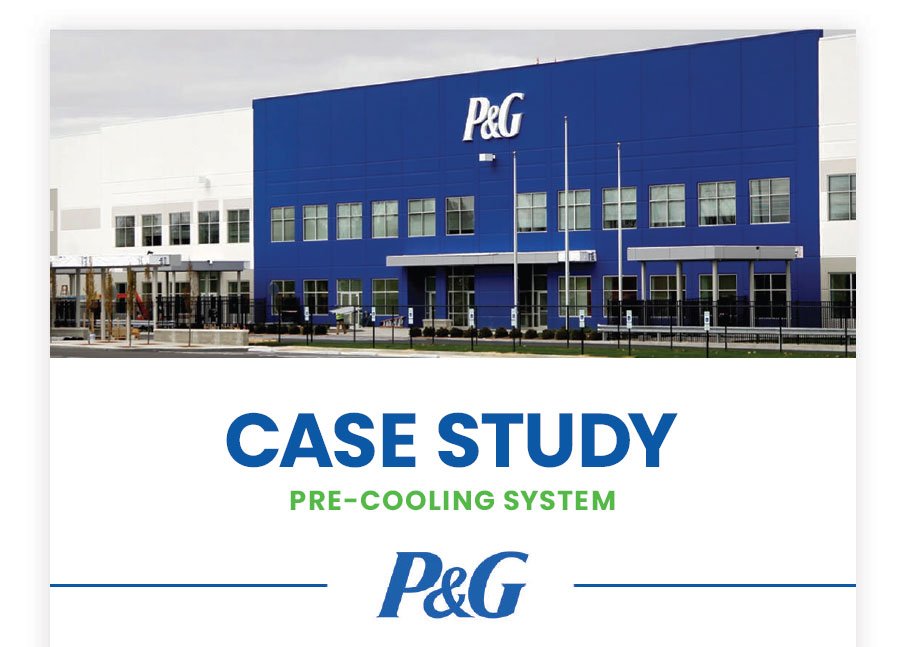
P&G Leveraged Our Expertise To Enhance Their Energy Efficiency, Offering A Model For Other Companies Looking To Reduce Costs And Improve Sustainability In Their Operations
P&G – PRE-COOLING SYSTEM
PROJECT HIGHLIGHTS
Savings In Electricity Consumption Per Month
₹4,00,000
Total Investment In Our IEC Module
₹32,00,000
Payback Period
Just 8 Months
Savings In Carbon Emission Per Year
7 Lac Tonnes Of CO2
OVERVIEW
- P&G’s Baby Care Product Plant In Hyderabad
- Significant Energy Consumption Due To Large-Scale Operations
- Trying To Procure A Cooling Solution Cost-Efficient & Sustainable
GOAL
Reduce Energy Consumption Cost
While Maintaining Optimal Conditions
CHALLENGE
Sustainable Cooling To Maintain The Necessary Environmental Conditions.
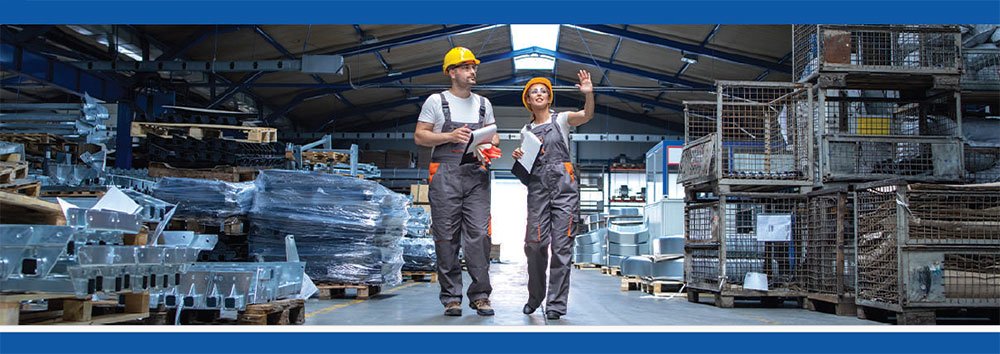
Currently Installed Setup
AHUs Installed
36,500 CFM x 3 Units
109,000 CFM Total
Fresh Air Requirement
75,000 CFM
Total Heat Load
1,055 KW
Existing Chiller Capacity
300 TR
SOLUTION
We Introduced An Innovative Indirect Evaporative Cooling (IEC) Module To Pre-cool The Fresh Air Before It Entered The Existing Air Handling Units (Ahus).
This Solution Involved
IEC Module Installed
25,000 CFM
x 3 Unit
Total Heat Removed
Through IEC Module
63 TR
Total Chiller Load
Saving
21%
The IEC Module Efficiently Pre-cooled The Incoming Fresh Air, Significantly Reducing The Load On The Existing Chillers.
RESULTS
The Implementation Of Evapoler’s IEC Module Led To Substantial Energy Savings
Energy Cost Reduction
25%, translating to a savings of ₹4,00,000 per month in electricity consumption.
Improved Operational Efficiency
The reduced load on the chillers not only saved energy but also prolonged the lifespan of the equipment.
Sustainability
The solution aligned with P&G’s commitment to sustainability by reducing the overall carbon footprint of the plant.
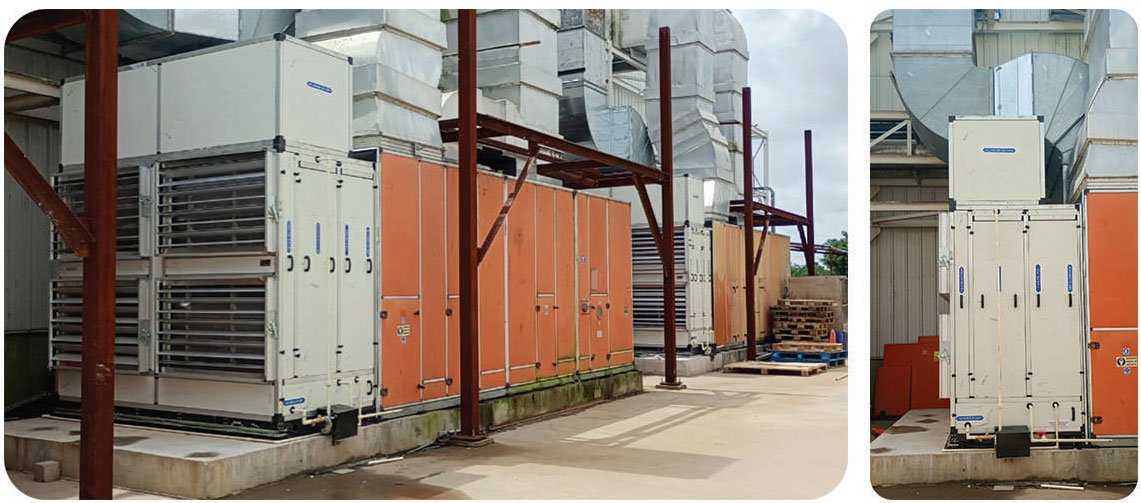